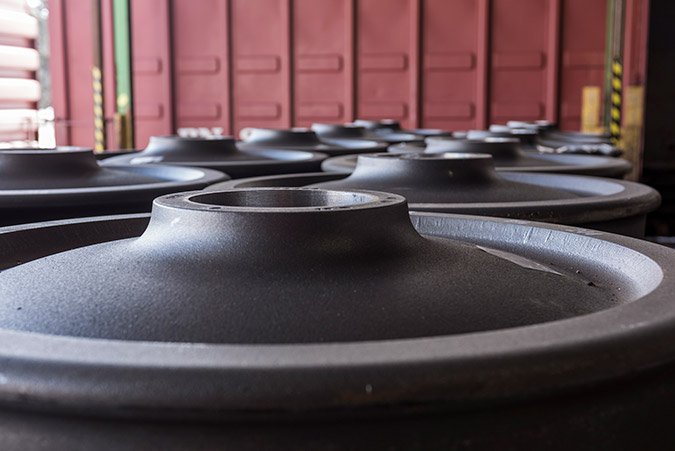
The Wheels at Havelock go ‘round and ‘round
The mechanical shops in Havelock, Nebraska, were established in 1891 by the Chicago, Burlington & Quincy railroad and have always been an important part of the northeastern Lincoln community as well as an integral part of keeping BNSF operations running. In 1978, the Havelock shops opened the present-day wheel plant to produce wheelsets used to keep railcars operating throughout our network. Recently, the shop produced its 3 millionth wheelset, a milestone resulting from hard work, advancements in technology and some good old fashioned pride in workmanship.
“The Havelock Wheel Shop is an integral part of the Havelock community. When you think of Havelock, you think of the wheel shop,” said State Senator Adam Morfeld. “It's an actual community and a family.”
Today, the wheel shop is the last of its kind among all U.S. Class 1 railroads and produces between 400 and 500 wheel sets each day. While wheels are not forged at the shop, they are assembled, repaired and reworked to be used on railcars.
To assemble the wheels, employees called machinists take the axles, loose wheel plates and bearings and fit them together using a wheel press. Each component must be bored to a specific tolerance and temperature before they can be fitted properly.
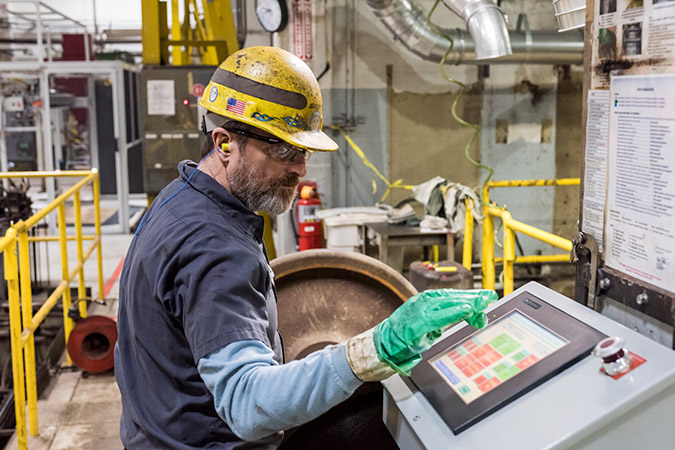
New technologies and automated processes have shortened the length of time between each millionth milestone. The one millionth milestone was in 1994 followed by the two millionth in 2008. Previously, every wheel had to be loaded in by hand and measured. Then, the wheels would be hand-lead to the front of the press where a machinist was ready to press them onto the axles.
“The one thing that sets Havelock apart from any other mechanical facility that I've been at is the automation and the innovation,” said Shop Superintendent Ward Greisen.
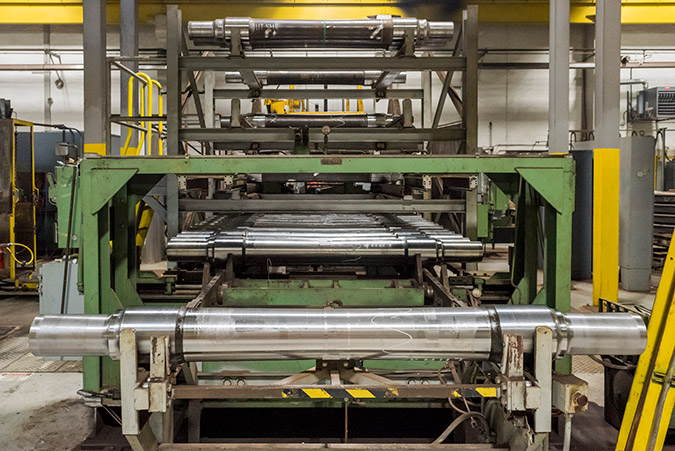
For example, the shop has an automated system where a crane loads the axles and measures them so that the wheel plate can be bored to the correct size. After that, the wheels are pressed on to the axle without human interaction. This process not only allows the data to be more precise and efficient, it’s made the entire operation even safer by limiting employees’ interactions with heavy wheels.
Because we produce our own wheels, we control the quality of the product, making our network safer by lowering the possibility of a wheel-related derailment. These processes have made Havelock an industry leader in wheel production and their methods, especially regarding quality control, are frequently adopted by other organizations, including the Association of American Railroads.
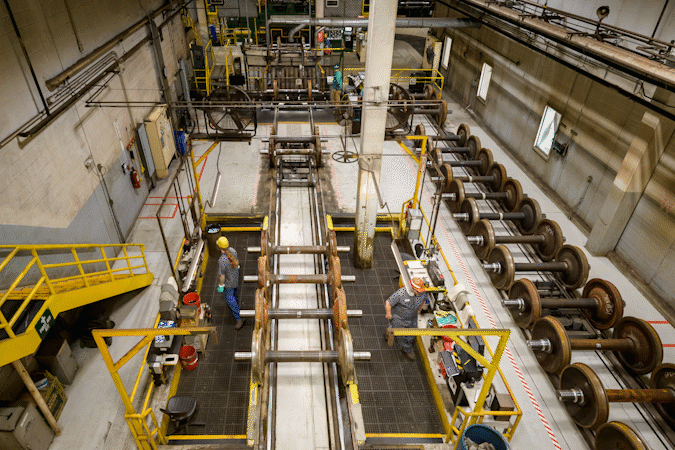
“I think having our own facility benefits us because we know that the wheels are produced to our own high standards,” said General Foreman Mike Anderson. “We know what we put into the wheels and wheelsets, and we get what we pay for -- and we can still do it at a competitive price.”
There are four different kinds of wheelsets produced by the wheel shop that fit a variety of different railcars and locomotives. In fact, approximately 90 percent of the wheels used by BNSF come directly from Havelock.
“When I see a train go by at a crossing, and I can spot the wheels that have come from our Havelock shop,” said Clint Hraban, electrical worker, “I feel a sense of pride knowing that those came from our hands.”
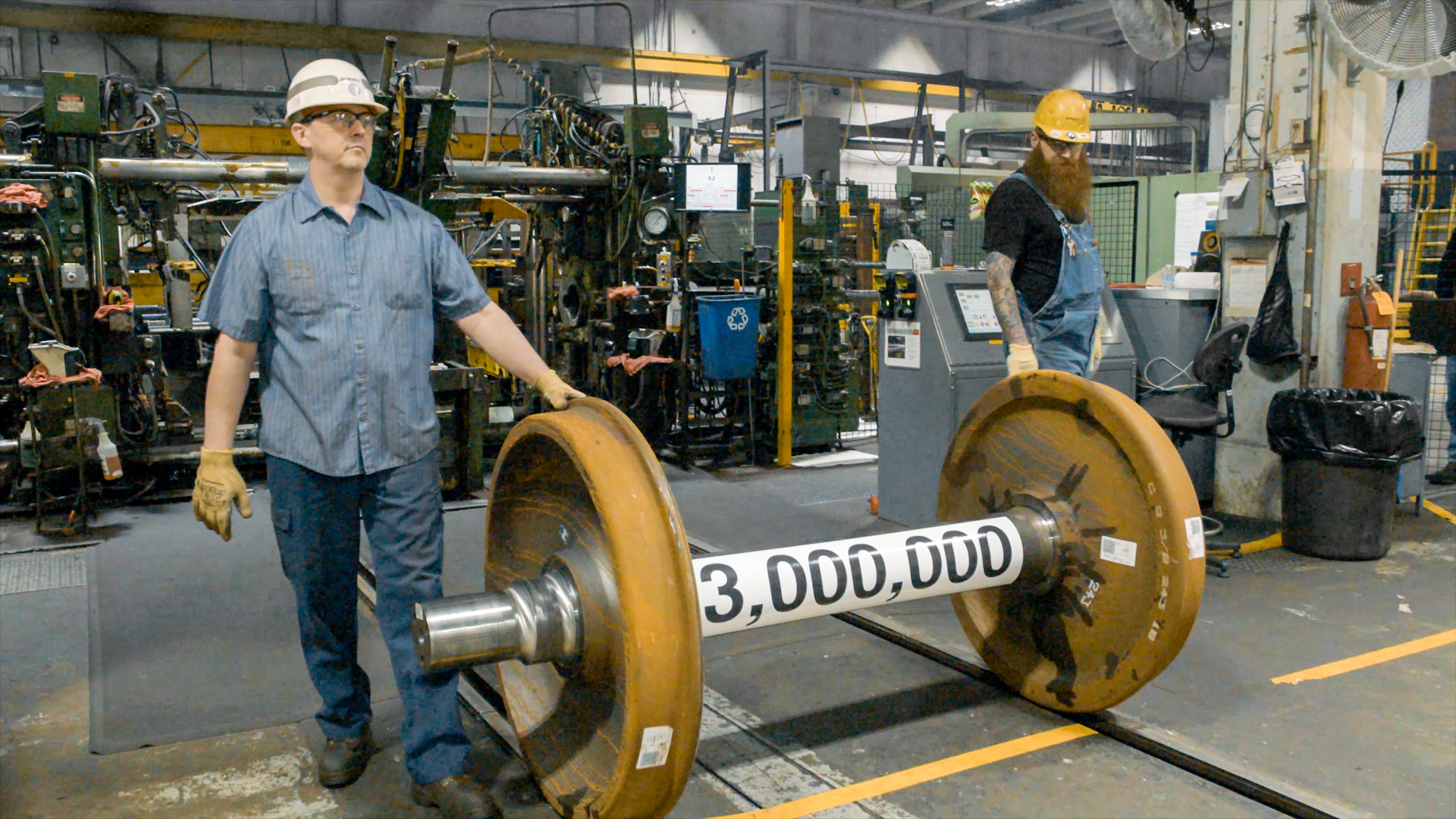
Do you have what it takes to work at Havelock?
Finding the right employees to work in a shop as unique as Havelock can prove to be a challenge as it takes a very particular experience to be qualified.
Last year, the wheel shop hired 21 new machinists, but it took a 6- to 7-months-long search to find the perfect candidates who could work with a variety of equipment and technologies, all while maintaining a safe work environment.
Employees who work at the shop do so with a lot of pride. Most spend the majority of their careers making sure our equipment is stocked with well-made, hand-crafted steel wheels so that we can get our customers’ shipments where they need to go without a wheel-related incident.
"It's a little bit like being an artist. You start with a block of something and end up with a sculpture,” said Machinist Dan Bowmaster. “There's some pride and some satisfaction in doing that and having it work the way it should.”